Series molds
What are series molds?
The series molds are a good option for the mass manufacturing since they are molds that are manufactured with high quality materials, offer cooling optimization, very precise movements and high performance, which allows our customers to obtain efficiency and profitability in its subsequent injection process.
The series molds are defined according to high durability parameters so that their design must always be optimal and guarantee the injection cycles defined with our customers. Therefore, each part – cores, mold bases, hot chambers, carts, ejectors, etc.,- is analyzed in detail avoiding possible interferences between them that can cause any problem during their life cycle.
Precisely during this definition phase, our team provides fundamental support thanks to the experience accumulated over the years in the design and subsequent development of the mold.
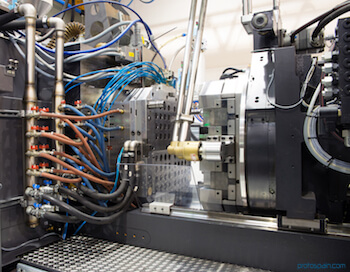
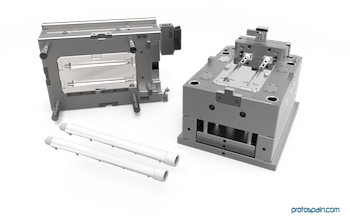
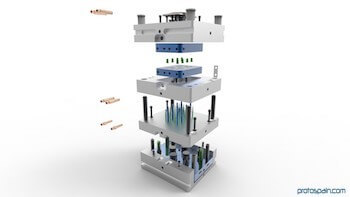
Differences between prototype molds and series molds
These are the main differences between prototype molds and series molds:
- Mold steel grade: Steel with enhanced durability
- Amount of impressions (cavities): Depending on the project
- Number of injections: > 1,000,000 cycles
- Quality of parts: Optimal
- Movement of carts: Automatic
- Chamber model: Hot chambers
- Lead time: Depending on the project
- Price: Depending on the project
- Mold steel grade: Steel with lower durability
- Amount of impressions (cavities): Generally, 1 or 2
- Number of injections: <100,000 cycles
- Quality of parts: Similar to series molds
- Movement of carts:: Manual
- Chamber model: Cold chambers
- Lead time: 10% less
- Cost: About 20% to 30% lower
Manufacturing process
- Quotation approval.- All mold manufacturing conditions are detailed here, and it must be signed and sealed by the client, and sent back to us in order to proceed with the next steps.
DFM.- Design For Manufacturing.- In this process, we analyze the part to be produced and we agree on the final design so the product can be injected seamlessly. This stage normally takes 2 or 3 days. - Mold Flow.- The injection flow in analyzed to determine the joint and injection points. This stage is carried out simultaneously with the previous one, and both take 2-3 days.
- 3D mold approval.-The mold design starts only when the DFM and the Mold Flow are approved by the client, and it will take around 4 days. The 3D files of the mold are sent to the client for approval.
- Manufacturing.- The mold is manufactured. During this period the client will receive a weekly report with the progress of the mold.
- Test.- When the mold is finished, in a 2 days led time, the first run of parts is made to be approved by the client.
- Later modificactions.- Required samples will be carried out for injection of parts final approval.
- Samples approval.- When the parts are approved, the mold will be ready for injection.
- Identification of the mold.- The molds will incorporate a nameplate with all the information that the client considers.